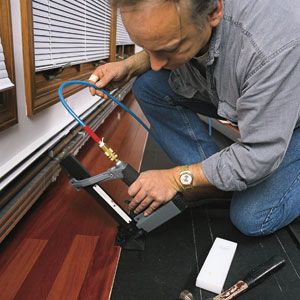
Engineered flooring seems like it ought to be cheaper than solid wood.
After all, the tongue-and-groove strips are made from plywood, with only the surface veneer (“wear layer”) cut from finish-grade maple, oak, cherry, or other hardwood. So customers are often shocked to discover that the manufactured planks may cost just as much as, or even more than, their solid wood counterparts. Still, homeowners and developers choose engineered products for 40 percent of new wooden floors, especially for remodeling jobs.
What’s the appeal? Imagine moving out of the family room for only 12 hours as a contractor pulls up the old wall-to-wall carpeting, then cuts
and assembles prefinished boards. No sanding, no waiting for multiple coats of polyurethane to dry. The floor is complete as soon as the boards are installed.
And these floors can be laid directly over a concrete slab; with solid
wood, a grid of 2x4s covered with plywood must first be installed over
the slab. This Old House contractor Tom Silva “floats” engineered floors over concrete, gluing the tongue-and-groove joints together, but not fastening the boards to the floor. Some products, designed for floors that won’t get wet, snap together and require no glue. Not being fastened down means the assembly can shrink and swell without cracking; a 1/2-inch expansion gap around the perimeter is hidden by baseboards or shoe moulding. When the subfloor is wood, the strips are simply glued or stapled down. Or, “you can float the floor over a 1/8-inch plastic foam insulation pad that’s stapled in place,” says Silva. “It makes things quieter downstairs.”
Not surprisingly, the growth of the engineered-wood-flooring market over the last quarter-century tracked the building boom in the Sun Belt
— where houses are built on concrete slabs. The product was invented in Europe shortly after World War II and first imported to the United States during the early 1980s by the Harris-Tarkett company. Popularity has grown steadily, and engineered wood flooring’s biggest appeal today is to homeowners who are living in the midst of renovations, since it eliminates on-site sanding and finishing. Remodelers may still have to contend with some fumes, however, because many of the installation glues that manufacturers recommend are urethane-based. This Old House chose engineered floors for the Santa Barbara, Milton, and Watertown projects. “It’s absolutely stunning, and it was so easy to install,” says Jan Winford, owner of the Santa Barbara home. “Since we were living here during the work, we didn’t want to deal with finishing the floors.”
Solid wood is available prefinished too, but the surface never winds up as flat as if the wood were sanded after being installed, and then
finished. In fact, prefinished engineered floors aren’t quite as even as floors that are sanded in place either, says Don Dickel, a third-generation wood-floor installer and finisher in Bangor, Maine. To hide slight irregularities in the surface, manufacturers mill a micro-bevel along each edge-creating 1/32- to 1/16-inch-deep grooves that are a telltale sign of an engineered wood floor.
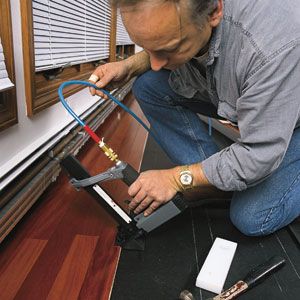
What Makes a Good Floor?
Some lines of engineered flooring effectively mimic real wood; others
are obvious fakeries. The key is whether the wear layer is rotary-cut or flat-cut. To make a rotary cut, the mill first soaks the log in water, then peels a thin layer off the circumference as it spins on a lathe. This generates the wide sheets of veneer used for plywood, and it gives engineered flooring the same distinctive wavy, repeating grain pattern that plywood has. Flat-cut veneer comes from a straight slice made directly along the log’s length. This veneer looks more like solid wood because it follows the grain, but since this type of cut yields less material per log, the veneer costs more than rotary-cut products.
Engineered flooring varies in its durability. Some kinds can be sanded and refinished when they become scratched and worn; others will need to be replaced. Cheap products may have just a 1/10-inch-thick surface veneer. Better products have one that’s 5/32- to 1/6-inch thick, which can withstand two sandings, extending the likely life of the flooring. Solid wood flooring, by comparison, typically offers about 5/16 -inch of wear layer above the tongue, enough to endure as many as seven sandings.
Consider, too, what’s under that top veneer. The tongue-and-groove board should contain at least three plys in all; five is even better, says
Jeff Hosking, a hardwood flooring consultant for This Old House.
“The more plys, the more stable the floor will be,” he says. That’s
because each layer is glued so that its grain runs at a right angle to
the layer above. And since wood tends to expand and contract across its grain as humidity changes, the movement of each ply is restricted when they’re glued in opposing directions. This alternating grain pattern makes an engineered floor more stable than a solid wood version; the joints in these floors won’t open into dust-collecting gaps in dry winter weather. The center core should also be made of real wood such as poplar, rather than a cheaper composite material, to provide a more stable base and a slight spring underfoot like solid wood.
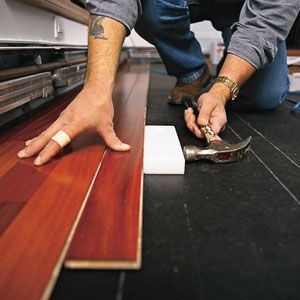
Engineered Options
The thinnest engineered wood flooring, just 3/8-inch thick, has little
inherent stability and must be nailed in place; 1/2-inch engineered
planks can be glued. Floating floors require 5/8-inch-thick planks,
according to Dickel.
The topmost veneer gets a factory finish, which is typically more
durable than painted-on polyurethane. Just two years ago, aluminum oxide coatings were introduced. This super-hard powder, which is also used in dental implants, ceramic faucet valves, and sandpaper, is added to the
urethane coating. “It’s difficult, if not impossible, to wear through
it,” says Thomas Brahler of Boa-Franc, an engineered-wood-flooring
manufacturer. At Boa-Franc, seven coats of aluminum oxide finish are
applied in less than five minutes, thanks to a speed-curing ultraviolet-light process developed in the 1980s. “The light creates a
chemical reaction within the finish that dries it in seconds,” says
Brahler.
Manufacturers guarantee aluminum oxide finishes for 25 years (versus a
likely life of 10 years for three coats of polyurethane). But Hosking has read the fine print: “It means that in 25 years there will still be something there protecting the wood from water,” he says. “But no finish protects against scratches and dents.”
The best approach to maximizing floor life is to treat it as if it
cannot be sanded, says Silva. That means keeping it clean, so dirt
doesn’t grind at the surface. “And keep your eye on it,” he says. “If
the finish seems to be wearing, give it a light sanding to scuff up the
surface, and then add a fresh coat of polyurethane. I always recommend
servicing the finish, not the floor.”
Selecting the best engineered wood flooring means paying the high end of the material’s price range of $6 to $11 per square foot. Add in
installation, about $2 to $4 per square foot, and the total price might exceed the installed price of a solid wood floor of the same species. So engineered flooring is probably best only under circumstances that make it more practical than wood. “If it’s your current dining room and you’ve got cats, go with prefinished engineered,” says Dickel. “If no one’s living there during the project, though, I’d choose traditional wood, finished in place.”
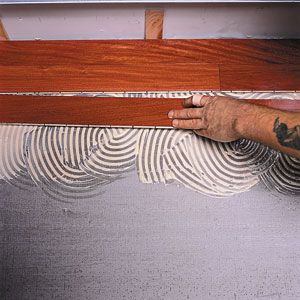
Grainy Pictures
Not all substitutes for solid wood floors are made from plywood. A
cheaper alternative, laminate flooring, gets its appearance from a
photographic image of wood. Glued to a fiberboard core, the picture is
protected on top by a clear finish. The resulting sandwich comes in
grooved panels. They’re installed with glue, much like engineered wood. Floor expert Jeff Hosking says laminate is more scratch-resistant than any wood floor — but once it does scratch, the damage is permanent. Laminate can’t be sanded. “I expect plastic laminate floors to last 8 to 15 years,” he says. “By then the homeowner gets tired of looking at the scratches and replaces the floor.” Hosking says laminate, which costs $2.50 to $5 per square foot (plus $2 or $3 per square foot for installation) can be a good choice in laundry rooms or bathrooms because it is highly water-resistant — if the glue is properly applied. The adhesive is what make the joints watertight. “If it isn’t done right, water can get down in the pressed board, and the floor will cup and curl,” he says.
Flooring Options
1 Its five plys offer dimensional stability, but this flooring has only a 1/16-inch surface veneer, which can’t be sanded and refinished when it’s scuffed.
2 Solid oak flooring , by comparison, has a 5/16-inch surface veneer (the wood above the tongue) and can be sanded up to seven times.
3 Some engineered flooring comes assembled in a panel for fast
installation, but still offers the appearance of narrow floorboards.
4 Planks that are 3/8-inch thick must be nailed in place…
5 …while planks with a 9/16-inch total thickness can be floated.
6 These six-ply boards have a hefty 3/8-inch birch top layer; note the beveled edges where the boards meet.